PRODUCT CATEGORIES
CONTACT US
DANBACH ROBOT JIANGXI.INC. Phone:+86-18602162995Tel:+86-0791-88133135
Fax:+86-0791-88221576
E-mail:info@dbhrobot.com
Address:No.811,Chuangxin 3rd road,High-tech district,Nanchang city,Jiangxi province,China
Welding robots Common Fault Analysis and Processing
DANBACH ROBOT
With the development of electronic technology, computer technology, numerical control and robotics, automatic arc welding robot workstations have been used in production since the 1960s, and their technology has become more and more mature. It has stable and improved welding quality, improved labor productivity, Strength, can work in a harmful environment, reducing the technical requirements of the workers to shorten the product replacement cycle of preparation and reduce the corresponding investment in equipment, etc., so in all walks of life has been widely used. However, there are some welding defects such as welding bias, undercutting, stomata and so on in the welding process. The welding robot may also have various faults in the long-term work. This paper mainly analyzes the welding defects and common faults.
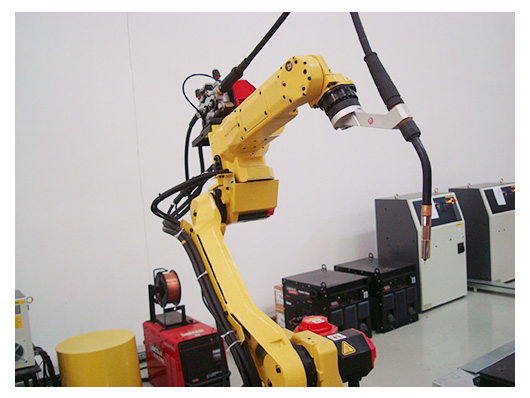
Common Faults and Their Solutions
(3) protection of gas monitoring alarm. Cooling water or protective gas supply is defective, check cooling water or protective gas line.
How to Protect Workpiece Quality
(2) the use of high precision assembly tooling to improve the accuracy of the weldment assembly.
(3) Weld should be clean, no oil, rust, welding slag, slag and other debris, allowing a solderable primer. Otherwise, it will affect the arc success rate. Positioning welding welding by the electrode to gas welding, while the spot welding parts to avoid residual welding residue welding residue or stomata, so as to avoid the instability of the arc or even the emergence of splash.
Requirements for welding wires for welding robots
Robots can be selected according to the needs of barrels or disc welding wire. In order to reduce the frequency of replacement of the wire, the robot should use barrels of wire, but the use of barrels of wire, wire feeding hose is very long, large resistance, welding wire stiffness and other high quality requirements. When using less copper wire quality, the copper surface due to friction off the friction tube will result in reduced volume, high-speed wire feeding resistance increases, the wire can not be sent out smoothly, resulting in jitter, the arc instability, affecting the welding Seam quality. Severe, there stuck phenomenon, so that the robot shut down, it is necessary to promptly clean up the wire tube.
Previous:none
next:Unmanned robotic handling storage logistics industry to prom