PRODUCT CATEGORIES
CONTACT US
DANBACH ROBOT JIANGXI.INC. Phone:0086-18801818975Tel:0086-0791-88133135
Fax:0086-0791-88221576
E-mail:info@dbhrobot.com
Address:Nanchang High - tech Zone Innovation No. 811
The operation process of AGV trolley in intelligent warehouse
DANBACH ROBOT
1. Enter the sorting code area operation
When the goods are transported by car to the warehouse, the car aligns the tail to the unloading point and matches the AGV trolley's path. At this time, the control center issues the AGV trolley near the mission dispatch to the unloading point, and the AGV trolley transports the full cargo to the cargo storage conveyor line according to the preset driving route. Because the number of AGV cars is limited, and the number of goods in the warehouse is large, each AGV car will complete the task of “pick-and-place” in a cyclical manner. In addition, the AGV trolley transports the empty pallets of the Chengyu to the empty pallet splitting equipment for splitting, ensuring that the cargo and the pallet supply are followed up at the same time.
2. Intelligent transfer area operation
The work of the intelligent transfer warehousing area is automatically completed by the AGV trolley. After the pallet is completed, the AGV trolley takes the entire pallet from the interface and transports it according to the pre-layed running route, transporting the entire pallet to the storage area interface. Since there are multiple outlets and interfaces of the whole pallet, each AGV trolley takes out the goods from the designated interface of the delivery sorting disc area according to the instruction of the control management system, and then automatically runs to the interface of the warehouse area set by any system. The automatic sorting and conveying of the whole pallet is completed. At the same time, the whole operation process is carried out under the coordination of the control and management system, ensuring smooth traffic and orderly operation, improving the efficiency of the transshipment operation and increasing the flexibility of the whole system.
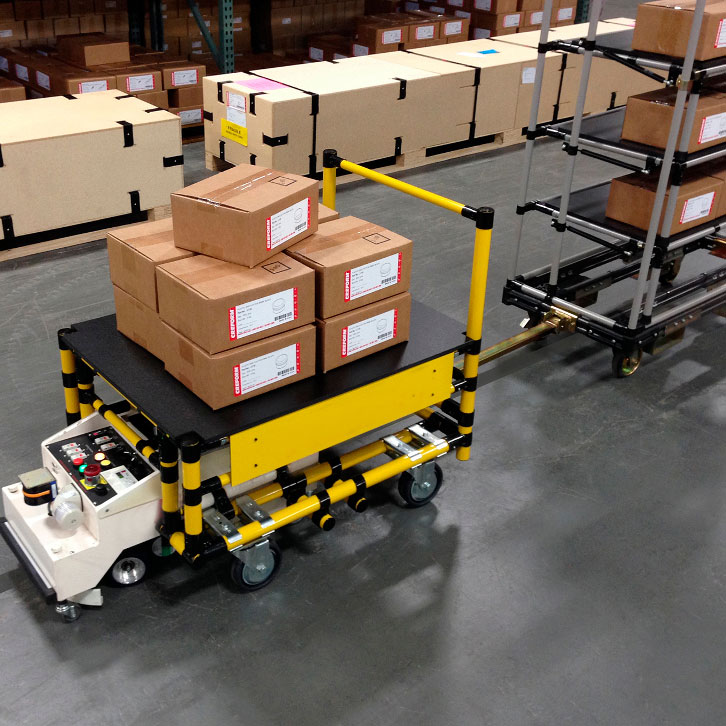
3. Intelligent output area operation
The operation of the intelligent transfer out of the warehouse area is also completed by the AGV car. According to the operation instructions issued by the control management system, the AGV trolley takes the whole pallet cargo from the driving to the outbound chain machine according to the pre-defined route, and then transfers to the automatic unloading delivery area interface. There are also multiple interface interfaces and unloading and delivery areas of the transshipment area. The AGV car can take out the goods from the designated interface under the command of the system, and then automatically run to the system-set warehouse area interface. The automatic sorting and conveying of the whole pallet, under the control of the traffic management system, the AGV trolley strictly follows the prescribed path, independently driving and working independently, and can also give the car to each other, increasing the fluency and flexibility of the operation.
4. Automatically disassemble the shipping area operation
The goods out of the warehouse are transported by the telescopic belt conveyor to the tail of the delivery vehicle. According to the “near principle”, the control system arranges the nearest AGV trolley to arrive at the rear of the car according to a preset path, and the goods on the telescopic belt conveyor are removed and neatly arranged. The stacking of the sequences into the compartment avoids manual stacking and improves work efficiency. The empty pallets and zero pallets after the goods are disassembled are completed by the AGV trolley. The entire process can achieve unmanned operation and improve the intelligent level of warehouse operations.
Previous:Advantages of Danbach AGV robot automatic transmission
next:Intelligent agv robot for material handling